Nenhuma imagem disponível na galeria.
Um pacote de incentivos às exportações brasileiras foi anunciado nesta quarta-feira (5) pelos ministérios da Fazenda e do Desenvolvimento, Indústria e Comércio Exterior. Entre as medidas, destaca-se a devolução com maior agilidade dos créditos do Programa de Integração Social (PIS), da Contribuição para Financiamento da Seguridade Social (Cofins) e do Imposto sobre Produtos Industrializados (IPI).
Os créditos tributários acumulados serão devolvidos em até 30 dias. Para isso, as empresas precisam ser exportadoras há pelo menos 4 anos e ter vendido para o exterior 30% do faturamento nos últimos dois anos, explicou o ministro da Fazenda, Guido Mantega.
Também será criada uma instituição voltada para estimular o comércio para outros países. A Eximbank será subordinada ao Banco Nacional de Desenvolvimento Econômico e Social (BNDES) e, inicialmente, operará com os recursos de financiamento à exportação existentes no banco.
O pacote prevê ainda a modernização do sistema público de garantias, através da criação de duas instituições. Uma delas é o Fundo Garantidor de Infraestrutura (FGIE), que unificará a atuação dos fundos naval, de energia e de parcerias público-privadas (PPPs). A segunda é a Empresa Brasileira de Seguros (EBS), que não concorrerá no mercado, responsável pela administração de riscos de fundos nos quais a União é cotista e para concessão de seguros não cobertos pelo mercado.
As pequenas e médias empresas também serão beneficiadas. A partir de agora, as receitas obtidas com as exportações não serão incluídas no limite do Simples Nacional, que contempla empresas com faturamento de até R$ 2,4 milhões por ano. Dessa forma, elas poderão exportar sem comprometer os critérios de adesão ao sistema simplificado de recolhimento de tributos.
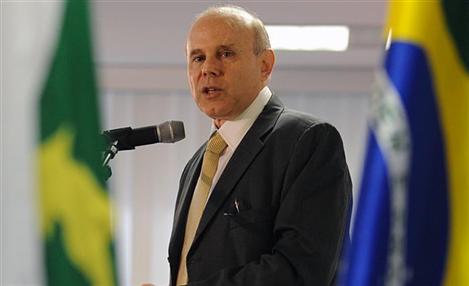